不干膠標(biāo)簽的供應(yīng)鏈相對較長,生產(chǎn)材料較多,印刷、貼標(biāo)應(yīng)用環(huán)境復(fù)雜,這就需要有好的設(shè)備、穩(wěn)定的生產(chǎn)工藝、優(yōu)良的原材料、性能優(yōu)異的膠水和硅油各方面的組合才能生產(chǎn)出一張優(yōu)質(zhì)的標(biāo)簽。然而,在日常生產(chǎn)過程中,一些產(chǎn)品問題如排廢不良、印刷白點、套印不準(zhǔn)、貼標(biāo)起翹、貼標(biāo)鼓泡等經(jīng)常令客戶困擾不已。本文,筆者通過一些實際案例分享對貼標(biāo)過程中的貼標(biāo)鼓泡、膠水殘留、出標(biāo)不暢等問題作下分析,并適當(dāng)給出對應(yīng)的解決方案,以饗讀者。
材料貼標(biāo)后導(dǎo)致起泡的原因比較復(fù)雜,通常潮氣較大,材料挺度不夠,被貼物表面粗糙不平、凹坑等不規(guī)則表面,膠水流平性不佳等原因均有可能導(dǎo)致標(biāo)簽起泡,這就需要制定專項的解決方案。
比如,2015年10月,西南某一標(biāo)簽印企客戶在使用80g銅版紙格底熱膠產(chǎn)品時碰到了標(biāo)簽起泡問題,標(biāo)簽起泡的區(qū)域被按下后一段時間又重新鼓起,給客戶造成了一定的困擾,如圖1所示。經(jīng)觀察發(fā)現(xiàn),該客戶的貼標(biāo)環(huán)境較差,濕度較高,達到了80%以上,且該客戶的貼標(biāo)方式為手工貼標(biāo),瓶體形狀也不規(guī)則,在使用不同廠家的材料時均有起鼓現(xiàn)象發(fā)生,但沒有覆膜的材料影響會比較小。這是由于標(biāo)簽是手工貼標(biāo),格拉辛底紙材料在放置后卷曲會比較嚴(yán)重,導(dǎo)致標(biāo)簽貼標(biāo)時不平整,從而產(chǎn)生起鼓現(xiàn)象。最后,建議這家客戶采用了PEK底材料,避免材料揭下時不平整;面材采用上光油方式處理,降低材料挺度;更換更加規(guī)則的瓶體,該問題得到了緩解。
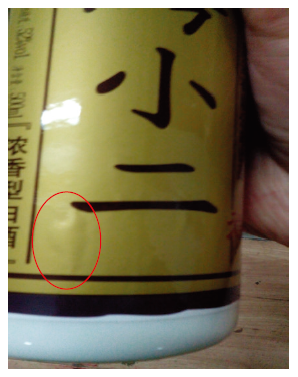
再比如,我們知道日化類產(chǎn)品在應(yīng)用過程中需要擠壓使用,對材料的選擇要求極為嚴(yán)格,且需要根據(jù)不同的貼標(biāo)表面選擇相應(yīng)的材料,如果采用匹配性能較差的材料,則出現(xiàn)問題的概率會大大增加,如圖2所示。通常,選擇常用的PE材料是解決方案之一,但透明PE材料的透明度較低,不能體現(xiàn)無感標(biāo)簽的效果,因此選擇可擠壓的PP材料是一些大品牌的最優(yōu)選擇。2020年冠豪開發(fā)了可擠壓型PP,目前已開發(fā)F4567(透明)、F1280(白色)兩種材料,經(jīng)測試,在擠壓瓶體上貼標(biāo)后反復(fù)擠壓,無起翹或鼓泡產(chǎn)生。
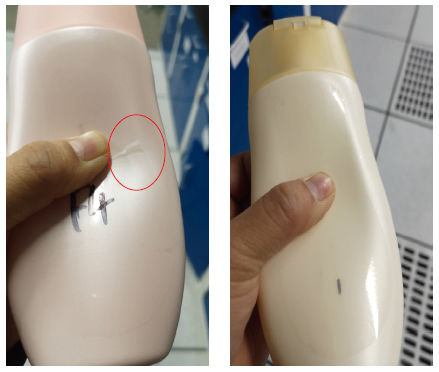
所謂膠水殘留,又稱殘膠,通常是指膜類標(biāo)簽在重貼撕開時出現(xiàn)的膠水殘留現(xiàn)象,尤其是膜類可移除類產(chǎn)品。2017年,華東的某一客戶在使用合成紙水性可移除貼膠卡片時曾出現(xiàn)過膠水殘留的情況(如圖3所示),當(dāng)時經(jīng)分析發(fā)現(xiàn)可移除膠水的粘性較弱,而被貼物為極性材質(zhì),膠水與被貼物的剝離力高于膠水與面材的剝離力,從而導(dǎo)致標(biāo)簽?zāi)z水殘留現(xiàn)象。最后該客戶使用了帶底涂面材的產(chǎn)品,增加了膠水與面材的結(jié)合力,緩解了膠水殘留的難題。
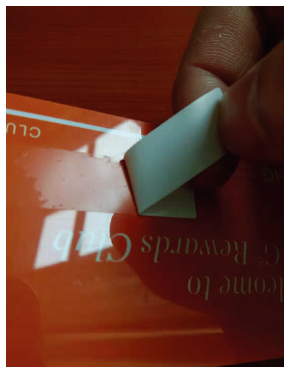
在貼標(biāo)過程中,通常會產(chǎn)生飛標(biāo)、出標(biāo)不暢的現(xiàn)象,其中出標(biāo)不暢通常是指離型力偏高或在模切加工過程中破壞硅油面,導(dǎo)致膠水滲透造成。筆者曾在2019年拜訪某客戶時碰到該客戶在貼標(biāo)過程中出現(xiàn)了部分標(biāo)簽不能出標(biāo)的問題(如圖4所示),首先我們測試了標(biāo)簽的離型力,發(fā)現(xiàn)數(shù)值偏高,然后又查看了硅油面,發(fā)現(xiàn)硅油面被破壞,導(dǎo)致膠水向底材滲透,最終使得標(biāo)簽不能順暢出標(biāo)。最后給到客戶的建議是:降低標(biāo)簽的離型力,調(diào)整模切深度,避免硅面被破壞,問題得到很好地解決。
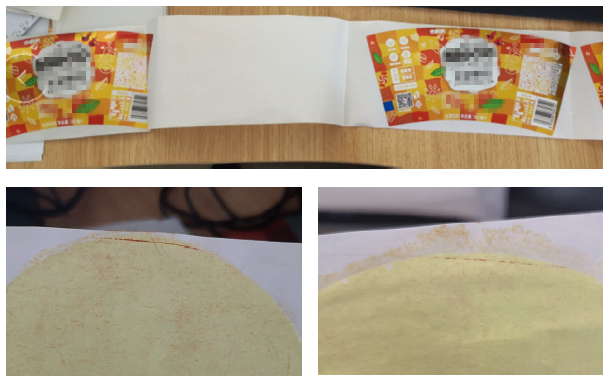
在貼標(biāo)過程中,也經(jīng)常會遇到底紙斷裂的情況,通常是由于底紙選材較薄、模切過深、硅油涂布缺陷、印刷加工工藝不當(dāng)?shù)确矫娴脑蛴绊?。曾?jīng)有某客戶就遇到過底紙斷裂異常的問題(如圖5所示),測試印后標(biāo)簽離型力,發(fā)現(xiàn)數(shù)值偏高,經(jīng)了解發(fā)現(xiàn)客戶采用了殺膠工藝,殺膠劑與硅油層發(fā)生了反應(yīng),再查看硅油面,發(fā)現(xiàn)硅油面有部分的雜質(zhì)點,造成了標(biāo)簽局部粘結(jié)現(xiàn)象。最后建議客戶調(diào)整了底紙的硅油配方,避免與殺膠劑的反應(yīng);更換了原材料,避免因材料影響,妥善解決了這一難題。
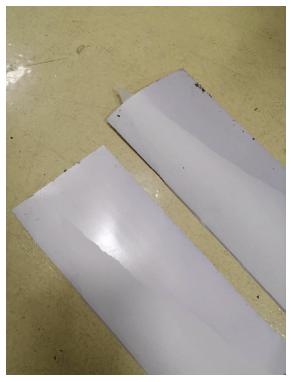