零成本改造,根本上解決凹印氣泡,產(chǎn)品不合格率降為零!
時(shí)間:2021-12-10 來源:
眾所周知,凹印油墨為液體油墨,采用泵壓循環(huán)供墨,過程中不可避免會(huì)產(chǎn)生氣泡,進(jìn)而影響印品質(zhì)量。特別是隨著環(huán)保政策的日益嚴(yán)苛,以及產(chǎn)品衛(wèi)生安全要求的不斷提高,水性油墨的使用比例不斷增加,尤其是水性雪花油墨、水性啞光油墨等的廣泛應(yīng)用,使得氣泡問題表現(xiàn)得更加突出,嚴(yán)重影響印刷質(zhì)量(如圖1)。本文,筆者以我公司“紅塔山(新時(shí)代)”煙包產(chǎn)品為例,分析凹印水性油墨氣泡的產(chǎn)生原因以及解決方案。
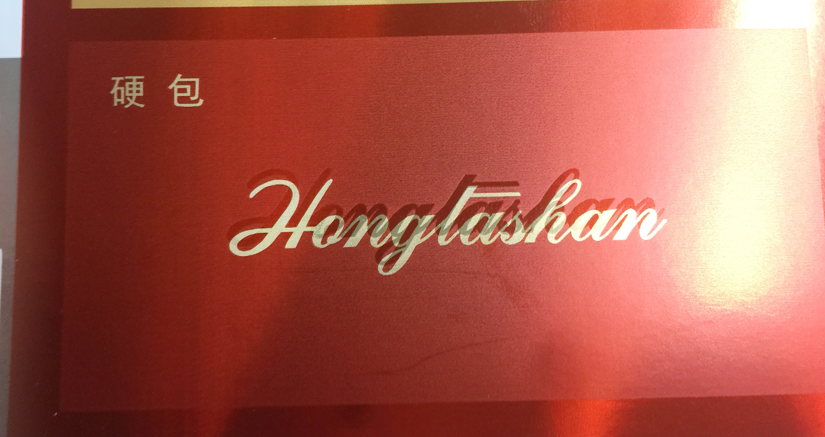
凹印水性油墨氣泡產(chǎn)生的主要因素包括油墨、供墨系統(tǒng)和操作因素。
(1)水性油墨使用水性樹脂連接料和以水為主的稀釋劑,水的表面張力和極性與有機(jī)溶劑有著較大的差異,加大顏料分散難度,必須使用表面活性劑類助劑改善樹脂和水以及顏料和樹脂的親和力。理論認(rèn)為,這些物質(zhì)在受力運(yùn)動(dòng)中,相對(duì)于有機(jī)類物質(zhì)更容易與空氣進(jìn)行交換,使氣體進(jìn)入運(yùn)動(dòng)的混合液中。
(2)消泡劑的使用可以消除油墨表面堆積的氣泡,卻無法消除油墨內(nèi)部的氣泡。
(3)油墨中的顏料對(duì)油墨中的氣泡具有吸附作用。
(4)油墨制造工藝和材料的改進(jìn)可以減少氣泡的產(chǎn)生,但無法完全避免。
(5)印版等固體物質(zhì)對(duì)氣泡具有吸附作用,致使印刷品表面更易產(chǎn)生印刷質(zhì)量問題。
(1)油墨泵的功率、轉(zhuǎn)速、葉片形狀等因素,都會(huì)對(duì)氣泡數(shù)量產(chǎn)生影響,在保證印刷供墨量的前提下,盡可能減少攪拌動(dòng)作,以降低氣泡數(shù)量,但不循環(huán)供墨,會(huì)導(dǎo)致油墨沉淀,分散不均勻,造成印刷色相不穩(wěn)定。
(2)輸墨管的管徑要與油墨泵的功率及供墨量匹配,減少泵墨的沖擊力度,可減少氣泡的產(chǎn)生。
(3)不論是噴淋式供墨裝置,還是浸泡式供墨裝置,泵上去的墨短時(shí)間內(nèi)會(huì)接觸旋轉(zhuǎn)的印版,可以根據(jù)印刷車速計(jì)算出接觸到刮墨刀的時(shí)間,在這么短的時(shí)間內(nèi),如果沒有完全自然消泡的過程,刮墨刀就會(huì)直接擠破氣泡,造成印品表面局部缺墨的印刷故障。
(4)為了保護(hù)印版并保證上墨量,上墨裝置與印版直接接觸或只能采用毛刷之類的軟物質(zhì)與印版接觸,中間的間隙或接觸的壓力不足以完全擠破油墨中的氣泡,而部分氣泡被擠破后形成的缺墨部分,也無法及時(shí)補(bǔ)充油墨。
(1)油墨黏度的控制。不同黏度的油墨在使用過程中與油墨泵葉片產(chǎn)生的沖擊力度不一樣,從而產(chǎn)生不同數(shù)量的氣泡;反之,取樣量杯內(nèi)油墨的氣泡數(shù)量會(huì)給油墨內(nèi)部結(jié)構(gòu)帶來變化,從而影響?zhàn)ざ鹊膶?shí)際測(cè)量結(jié)果,給操作人員帶來誤判。
(2)溶劑配比的準(zhǔn)確性。凹印油墨的溶劑主要采用乙酸乙酯、乙酸正丙酯、乙醇、水等物質(zhì),根據(jù)油墨的不同性質(zhì)選用不同配比的溶劑作為稀釋劑,這些物質(zhì)的表面張力不同,氣泡數(shù)量就會(huì)有所不同,水是氣泡產(chǎn)生的主要因素。
(3)上墨裝置的調(diào)整及安裝的精細(xì)程度。上墨裝置與印版之間的間隙、上墨裝置自身的水平度等都會(huì)影響油墨循環(huán)使用過程中氣泡的產(chǎn)生及自主消泡的程度。
(4)泵墨量的控制。在保證印刷供墨的前提下,通過閥門或回流閥的控制,泵墨量越小,氣泡數(shù)量越少,這需要操作人員仔細(xì)操作。
針對(duì)氣泡產(chǎn)生原因,技術(shù)人員進(jìn)行多角度試驗(yàn),以尋求最佳解決方案。
(1)與多家油墨供應(yīng)商溝通,試圖從油墨材料方面改進(jìn),主要是樹脂連接料的選型和改進(jìn),特別是對(duì)水性油墨的改進(jìn),但氣泡問題一直沒有徹底解決。
(2)消泡輥在凹印設(shè)備上很難固定安裝,且消泡效果不理想。
(3)油墨車上改造添加印版浸泡裝置,增加油墨靜置消泡時(shí)間,但改造設(shè)備難度較大,且消泡效果仍不理想。
(4)對(duì)上墨系統(tǒng)進(jìn)行改進(jìn),包括改造噴墨孔,避免油墨直噴到印版上,減少氣泡數(shù)量;改造回墨路,減少油墨流動(dòng),調(diào)節(jié)上墨裝置與印版的間隙,盡量擠破氣泡等多項(xiàng)措施。
(5)試用不同功率、管徑、葉片形狀的油墨泵。
(6)調(diào)整油墨黏度、溶劑配比。
(7)加入不同比例的消泡劑,并對(duì)比試用。
經(jīng)過實(shí)踐證明,以上多種措施只能改善卻不能從根本上解決氣泡問題。結(jié)合氣泡的產(chǎn)生原因,我們認(rèn)為,既然目前無法從材料上解決油墨流動(dòng)時(shí)產(chǎn)生氣泡,就只能考慮物理方法。
初步計(jì)劃在油墨通過上墨系統(tǒng)覆蓋到印版上之后,在刮墨刀刮墨之前的狹小空間內(nèi),對(duì)覆蓋在印版上的油墨中的氣泡進(jìn)行碾壓擠破,并在碾壓后對(duì)擠破氣泡處補(bǔ)充油墨,保證印刷圖案上墨均勻。
實(shí)際生產(chǎn)中遇到較大版面的水性啞光油墨印刷時(shí),會(huì)出現(xiàn)嚴(yán)重的氣泡問題,甚至無法印出一張合格品,油墨供應(yīng)商的技術(shù)人員也無法解決。為此,我們計(jì)劃對(duì)上述解決方案的初步計(jì)劃進(jìn)行實(shí)施改造,具體過程如下。
該材料需具備抗水、抗溶劑性能,且具有一定的厚度與強(qiáng)度。經(jīng)過對(duì)比分析,我們決定就地選材,選擇厚度為0.125mm的片基,該片基不僅耐用,而且不會(huì)摩擦損壞印版。
不同印刷設(shè)備的上墨方式以及機(jī)械結(jié)構(gòu)有所不同,以我公司使用的尚邦GR830設(shè)備為例,考慮到碾壓印版表面所覆蓋油墨內(nèi)氣泡的力度和間隙、印版旋轉(zhuǎn)的方向、碾破氣泡處需繼續(xù)補(bǔ)充油墨的情況,決定在上墨架的勻墨刀片下面和印版具有一定接觸面積且力度較大的位置,加裝自制筒狀膠片,如圖2所示。
手動(dòng)檢測(cè)上墨效果與正常情況一致,預(yù)計(jì)可以正常生產(chǎn),如圖3所示。
上墨架上安裝好片基,開機(jī)驗(yàn)證氣泡問題明顯好轉(zhuǎn),只有零散氣泡問題。經(jīng)分析,仍需加強(qiáng)對(duì)吸附在印版表面氣泡的碾壓,并對(duì)碾破氣泡處補(bǔ)充油墨,因此對(duì)上述安裝的片基進(jìn)行了改進(jìn),在固定勻墨刀片的螺栓處再加裝筒狀膠片,起到對(duì)碾破氣泡處重新補(bǔ)墨的作用,如圖4所示。

改進(jìn)后再次開機(jī)試驗(yàn),不再出現(xiàn)氣泡問題,順利完成生產(chǎn),該批次印品不合格率從改造前的100%降為改造后的0%,印樣如圖5所示。
至此,基本確認(rèn)改進(jìn)后的氣泡處理裝置(如圖6所示)可以解決凹印水性油墨氣泡問題。
針對(duì)上述解決方案,我們后續(xù)進(jìn)行了驗(yàn)證,涉及5種主要凹印水性油墨滿版印刷產(chǎn)品的生產(chǎn)情況。
通過2個(gè)月、10個(gè)產(chǎn)品、500多萬印張的跟進(jìn)驗(yàn)證,所有產(chǎn)品均未出現(xiàn)氣泡問題,因此我們認(rèn)為該解決方案的實(shí)施有效解決了凹印水性油墨氣泡問題,完全符合大規(guī)模生產(chǎn)的需求,可明顯提高印品質(zhì)量,降低操作人員工作強(qiáng)度和工作量,節(jié)約原輔材料,產(chǎn)生巨大的經(jīng)濟(jì)效益和社會(huì)效益。
此外,我們還對(duì)片基材料進(jìn)行了標(biāo)準(zhǔn)化處理,設(shè)定上片基尺寸為130mm×840mm,下片基尺寸160mm×840mm,以便大規(guī)模生產(chǎn)使用。
作者:珠海經(jīng)濟(jì)特區(qū)誠成印務(wù)有限公司 許東升
編輯:宋慧慧